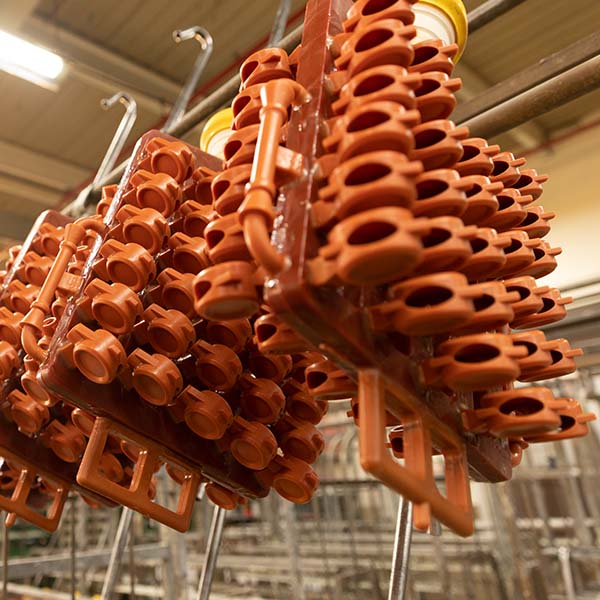
Investment Casting Process
- Step 1: Wax is injected into a die to produce a pattern
- Step 2: Patterns are affixed to a wax runner bar to create an assembly called a ‘tree’
- Step 3: A tree is dipped into a slurry to build up a ceramic shell
- Step 4: The wax is melted out of the shell using heat and pressure
- Step 5: The dewaxed ceramic shell is fired at 2000 degrees in a kiln
- Step 6: Metal is poured into the fired shell
- Step 7: The ceramic shell is knocked off the casting
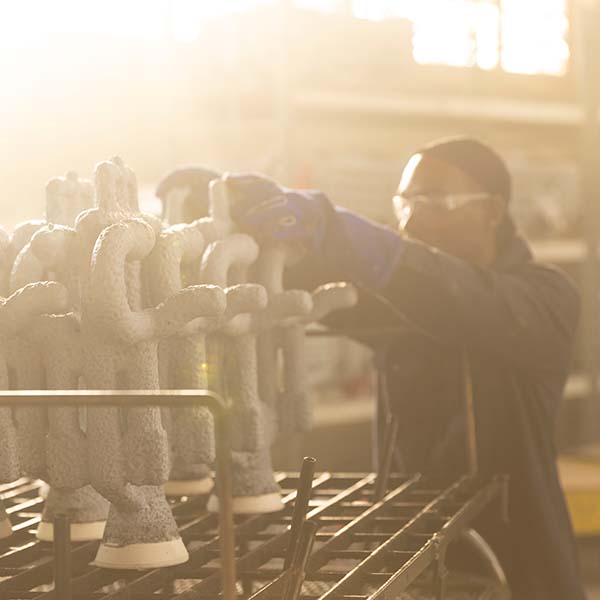
Investment Casting Capabilities
Sigma works with more than 200 alloys, including stainless steel, carbon steel, aluminum, brass, bronze, copper, nickel, and high-temperature alloys.
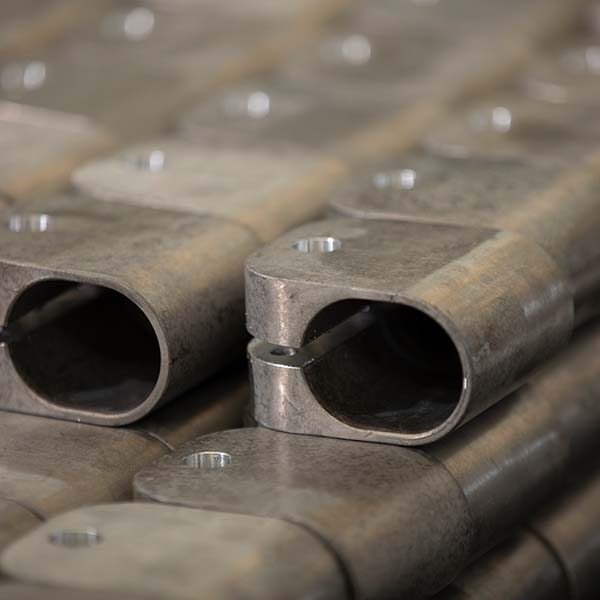
Investment Casting Applications
Part sizes typically range from 1 ounce to as much as 100 pounds and can be found in tough industrial applications such as power generation, oil & gas, fluid power, medical and dental, and aerospace and aviation.
Advantages
Investment casting creates precision products with high dimensional and geometric accuracy. Because near net-shape parts are created, investment casting saves time and money by reducing the need for secondary operations. Investment casting provides many advantages - it can achieve tighter dimensional tolerances compared to sand casting; shorter lead times; greater precision and accuracy compared to metal fabrication; and lower tooling costs versus forging.